Setting Safety Goals
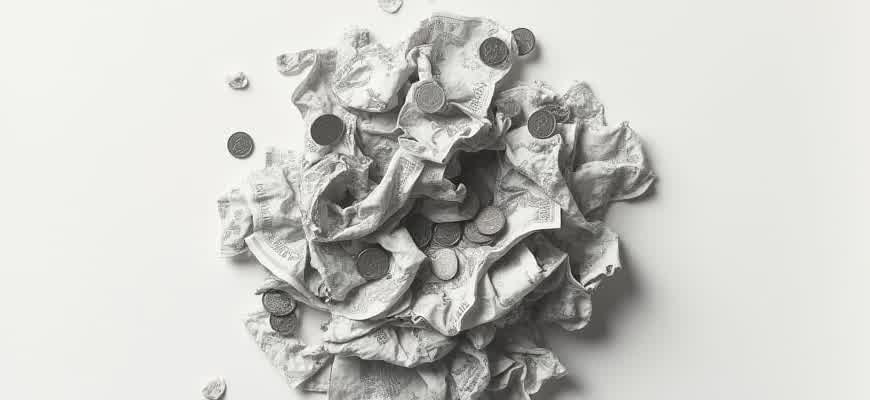
Setting effective safety targets is critical for ensuring workplace well-being and minimizing risks. A well-defined safety plan helps organizations focus on preventing accidents and fostering a culture of awareness among employees. By clearly outlining specific objectives, companies can measure progress and make necessary adjustments to improve safety standards.
Key Steps in Defining Safety Goals:
- Identify hazards and assess risk levels.
- Set measurable and attainable targets for accident reduction.
- Ensure all employees are trained and equipped to meet safety expectations.
- Monitor and evaluate progress regularly.
"A goal without a plan is just a wish." – Antoine de Saint-Exupéry
Example of Safety Goal Breakdown:
Objective | Target | Action Plan |
---|---|---|
Reduce workplace accidents | 10% decrease in incidents | Conduct regular safety training and implement new safety protocols |
Increase safety equipment usage | 100% employee compliance | Distribute PPE and perform regular equipment checks |
How to Set Safety Goals for Your Team
Establishing clear and achievable safety goals for your team is crucial to maintaining a secure and productive work environment. Effective safety goals help prevent accidents and injuries, while also fostering a culture of responsibility and awareness. These objectives should be specific, measurable, and aligned with the overall safety strategy of the organization. When setting goals, it’s important to engage with your team and ensure their active participation, as their input will make the goals more relevant and achievable.
To create meaningful safety goals, first assess the risks present in your workplace, then determine what actions will best address those risks. These goals should be specific enough to guide behavior, yet flexible enough to accommodate evolving safety needs. A good approach involves breaking down broader objectives into smaller, manageable targets that can be tracked and evaluated over time.
Steps to Setting Effective Safety Goals
- Identify Key Safety Areas: Assess risks such as equipment safety, hazard identification, or employee training.
- Involve Your Team: Gather input from employees to ensure their concerns and insights are considered.
- Set SMART Goals: Make goals Specific, Measurable, Achievable, Relevant, and Time-bound.
- Monitor Progress: Regularly review safety metrics to ensure goals are being met.
Example of Safety Goals Breakdown
Goal | Action | Timeline | Responsible |
---|---|---|---|
Reduce workplace injuries | Implement new safety training program | 3 months | Safety Manager |
Increase hazard reporting | Launch an anonymous reporting system | 1 month | HR Department |
Improve equipment maintenance | Perform monthly equipment checks | Ongoing | Maintenance Team |
“Safety goals should always reflect the priority of preventing harm while supporting employee well-being.”
Identifying Essential Safety Indicators for Your Sector
In every industry, the importance of safety is undeniable. However, to establish clear safety objectives, it is essential to define measurable safety indicators that will guide your organization. These indicators will allow you to evaluate performance, identify risks, and track improvements. The specific metrics you choose depend on your industry, the nature of your operations, and regulatory requirements.
Focusing on key safety metrics will not only ensure compliance but also create a proactive safety culture. It’s crucial to select the right indicators that reflect the safety health of your operations. Below are some essential metrics that industries often focus on to drive their safety performance.
Common Safety Metrics by Industry
- Incident Frequency Rate (IFR): Tracks the number of incidents (such as accidents or injuries) per a set number of work hours. Useful in high-risk sectors like construction or manufacturing.
- Lost Time Injury Rate (LTIR): Measures the number of days lost due to work-related injuries. Important for industries like logistics and heavy machinery.
- Severity Rate: Monitors the severity of incidents by calculating the number of lost workdays per incident. Crucial for sectors like mining or chemicals.
- Near Miss Reporting: Tracks incidents that did not result in harm but could have. This is key in aviation and healthcare industries.
- Employee Training Completion Rate: Measures how many employees have completed mandatory safety training. This is significant for sectors like oil and gas, where safety protocols are strict.
Example Table: Safety Metrics for Different Industries
Industry | Key Safety Metric | Importance |
---|---|---|
Construction | Incident Frequency Rate (IFR) | Tracks frequency of incidents on job sites |
Healthcare | Near Miss Reporting | Prevents accidents before they happen |
Manufacturing | Lost Time Injury Rate (LTIR) | Identifies trends in injury severity |
Oil & Gas | Employee Training Completion Rate | Ensures staff are adequately trained for hazardous environments |
Important Note: Always tailor your safety metrics to your specific operational risks, local regulations, and organizational needs.
Understanding Legal and Compliance Obligations
When setting safety goals within any organization, it is essential to have a comprehensive understanding of the legal and compliance framework that governs workplace safety. Various laws, regulations, and industry standards must be adhered to, as non-compliance can result in severe financial penalties, legal consequences, and damage to the company's reputation. By ensuring that safety goals are aligned with these requirements, businesses can create a safer environment and mitigate potential risks.
Compliance with legal and safety standards often involves understanding specific local, national, and international guidelines that apply to a given industry. This helps businesses create measurable and realistic safety objectives that also meet the required legal benchmarks. Incorporating these standards into safety goal-setting practices is crucial for maintaining a sustainable and legally compliant operation.
Key Legal Considerations
- Workplace safety regulations (e.g., OSHA in the United States, HSE in the UK)
- Industry-specific standards and certifications (e.g., ISO, NFPA)
- Employee rights and labor laws regarding safety (e.g., workers' compensation, reporting hazards)
- Local environmental laws impacting workplace operations (e.g., pollution control, waste disposal regulations)
Common Compliance Requirements
- Risk Assessments: Conducting regular assessments to identify potential hazards and mitigate risks.
- Training Programs: Ensuring that employees receive ongoing safety training and are familiar with emergency procedures.
- Documentation: Keeping accurate records of safety inspections, incidents, and compliance efforts.
- Audits: Regular internal and external audits to ensure compliance with safety regulations.
Essential Compliance Standards
Standard | Description | Impact on Safety Goals |
---|---|---|
OSHA | Occupational Safety and Health Administration regulations for workplace safety | Helps define safety protocols and establishes minimum safety requirements for various industries |
ISO 45001 | International standard for Occupational Health and Safety Management Systems | Guides organizations in managing safety risks and enhancing employee safety |
NFPA | National Fire Protection Association codes for fire safety | Ensures that fire safety protocols are met, reducing risks of fire hazards |
Important: Non-compliance with legal requirements can result in fines, legal action, and harm to an organization's reputation. It is vital to keep up with any updates to safety regulations to stay compliant.
Involving Employees in Setting Safety Goals
Creating a culture of safety begins with actively engaging employees in the process of defining safety objectives. When employees have a direct role in setting these goals, they are more likely to take ownership of the outcomes. This involvement fosters a sense of responsibility and enhances adherence to safety protocols on the shop floor. Additionally, employees possess first-hand knowledge of workplace hazards, which allows them to contribute valuable insights when safety targets are established.
Moreover, collaboration between management and staff encourages transparent communication and the identification of realistic, achievable safety goals. Setting these objectives as a team ensures that they align with the practical realities of day-to-day operations and supports a more effective safety program overall.
Key Benefits of Employee Involvement in Safety Goal Setting
- Increased Engagement: Employees feel more invested in safety when they contribute to goal-setting.
- Practical Insights: Workers bring real-world knowledge of hazards and risks, making safety goals more relevant and practical.
- Better Compliance: Employees are more likely to follow safety procedures they helped create.
- Enhanced Communication: Collaborative goal-setting encourages an open dialogue between employees and management.
Steps to Involve Employees in Safety Goal Setting
- Conduct Safety Surveys: Regularly ask employees for feedback on existing safety protocols and potential hazards.
- Hold Safety Meetings: Organize meetings where employees can discuss safety concerns and suggest improvements.
- Form Safety Committees: Create committees that include representatives from various departments to brainstorm and set safety goals.
- Provide Training: Ensure employees have the necessary skills and knowledge to participate effectively in goal-setting processes.
Involving employees in safety goal setting not only improves the safety culture but also empowers them to take responsibility for their own well-being and that of their colleagues.
Examples of Employee-Driven Safety Goals
Goal | Employee Contribution |
---|---|
Reduce Workplace Injuries | Employees identify specific risks and recommend preventive actions based on their daily experiences. |
Improve Hazard Reporting | Workers propose a more user-friendly reporting system to increase incident reporting frequency. |
Set Realistic and Achievable Safety Targets
When establishing safety objectives, it's crucial to ensure they are both realistic and achievable. Setting unattainable goals can lead to frustration and disengagement, whereas clear and feasible targets motivate progress and foster a culture of safety. By focusing on attainable milestones, teams can actively work towards reducing hazards and improving overall safety in a sustainable way.
Effective safety targets should be specific, measurable, and time-bound. These criteria ensure that safety goals are not only understood but also actively worked towards. Below are some steps and strategies to set achievable safety targets in any work environment.
Key Principles for Setting Achievable Safety Goals
- Understand the current safety performance – Before setting new goals, analyze the existing safety records and identify areas needing improvement.
- Involve employees in the process – Engaging staff in goal setting increases buy-in and helps identify realistic targets from the ground up.
- Use historical data – Past incidents and near misses can provide valuable insights into areas where safety measures need strengthening.
Steps to Define Realistic Safety Targets
- Assess the Risks – Start by identifying key risks in the workplace. This ensures safety targets address the most pressing issues.
- Break Down Goals into Smaller Objectives – Large goals can feel overwhelming. Break them down into smaller, manageable targets.
- Track Progress – Implement a system for monitoring progress regularly and adjusting goals when necessary.
- Ensure Support and Resources – Ensure the necessary tools, training, and support are available to achieve the targets set.
Setting safety goals that are too ambitious without adequate resources or a clear path can lead to setbacks, undermining morale and hindering progress. Focus on incremental improvements that align with the team’s capacity.
Example Safety Goal Table
Safety Goal | Measurement Criteria | Deadline | Responsible Party |
---|---|---|---|
Reduce workplace injuries by 10% | Injury rates (per 1000 hours worked) | 6 months | Safety Manager |
Complete safety training for 95% of staff | Training completion rate | 3 months | HR Department |
Track Safety Progress with Clear Indicators
Monitoring safety progress is crucial for ensuring the effectiveness of implemented safety measures. Clear indicators allow organizations to evaluate safety performance, identify areas for improvement, and measure the impact of safety interventions. These indicators should be specific, measurable, and relevant to the unique needs of the workplace. By setting these clear benchmarks, companies can move towards a safer environment with purpose and accountability.
To track safety performance efficiently, key metrics should be defined and tracked regularly. These can range from incident reports to employee training completion rates. Establishing a routine for measuring these indicators provides a consistent way to assess progress and highlight areas needing attention.
Types of Indicators to Track
- Incident Frequency Rates: Monitor the frequency of workplace accidents and near-misses.
- Training Compliance: Measure the percentage of employees who have completed mandatory safety training.
- Inspection and Audit Scores: Track results of regular safety inspections and audits.
- Employee Feedback: Collect safety-related feedback from staff through surveys and focus groups.
Setting and Measuring Safety Goals
- Define Clear Targets: Establish concrete and realistic safety goals, such as reducing incidents by a certain percentage within a year.
- Use Benchmarks: Compare safety data with industry standards or historical performance to set meaningful goals.
- Regularly Review Data: Consistently evaluate safety data and adjust strategies as needed.
Example Safety Indicator Dashboard
Indicator | Target | Current Status |
---|---|---|
Incident Frequency | Reduce by 10% | 7% decrease |
Training Compliance | 100% completion | 95% completion |
Inspection Score | Score 90+ | 87 |
Important: Tracking safety progress should not just be about collecting data, but about interpreting it in a way that drives improvement. Safety goals must be adjusted as new risks emerge and strategies evolve.
Conduct Regular Safety Audits and Reviews
Regular safety audits and reviews are essential for identifying hazards and ensuring that safety measures are properly implemented in the workplace. These assessments help pinpoint areas where safety protocols may be lacking or outdated. Regular checks can prevent potential accidents, reduce risks, and promote a safety-conscious culture among employees. By keeping safety practices under constant scrutiny, organizations can enhance their overall safety performance.
Conducting these audits involves examining both physical safety infrastructure and procedural practices. Safety audits should be scheduled periodically, ensuring that all areas are regularly assessed and that any emerging risks are addressed promptly. A review system allows the company to evaluate the effectiveness of current safety measures and make necessary adjustments to stay ahead of potential issues.
Key Steps for Effective Safety Audits
- Schedule audits at regular intervals.
- Involve various team members for a comprehensive evaluation.
- Document all findings and track corrective actions.
- Assess both equipment and employee safety practices.
Audit Review Process
- Conduct an initial inspection of safety conditions.
- Identify any risks or violations in safety protocols.
- Implement corrective actions where necessary.
- Reassess the safety situation after corrective measures are implemented.
- Prepare a detailed report on the audit and share findings with stakeholders.
Important: Regular safety audits and reviews help in maintaining a proactive approach towards safety, ensuring that issues are addressed before they result in accidents or injuries.
Sample Audit Checklist
Area | Inspection Criteria | Action Required |
---|---|---|
Workplace Equipment | Check for wear and tear, safety labels | Replace damaged equipment, update labels |
Employee Training | Review safety training records | Provide additional training if necessary |
Emergency Exits | Ensure exits are clear and accessible | Clear blockages, verify exit routes |
Incentivize Safety Goals to Drive Compliance
Implementing a system of rewards can significantly motivate employees to prioritize safety within the workplace. By providing tangible incentives, businesses can encourage workers to adhere to safety protocols and take proactive steps in preventing accidents. This not only boosts morale but also fosters a culture of safety where employees feel valued for their contributions to a secure environment.
When safety goals are tied to incentives, workers are more likely to engage with safety initiatives, leading to fewer incidents and a reduction in overall risk. Clear, attainable rewards create healthy competition, pushing individuals and teams to consistently improve their safety practices. Incentive programs should be designed to be both achievable and meaningful to encourage long-term participation.
Types of Incentives for Safety Goals
- Monetary rewards for achieving safety milestones
- Recognition programs such as "Employee of the Month" for safety achievements
- Extra time off or flexible working hours for consistent safety adherence
Setting Up Effective Safety Incentive Programs
- Define specific, measurable safety goals that employees can easily track.
- Determine what types of rewards will resonate most with your workforce.
- Communicate the program clearly, ensuring everyone understands how to participate and what the rewards are.
- Evaluate and adjust the program regularly to keep it relevant and motivating.
"A well-designed incentive program can be a game-changer in improving workplace safety. It transforms safety from an obligation into a shared goal that everyone can work toward."
Reward Program Example
Safety Achievement | Reward |
---|---|
Zero accidents in a quarter | $500 bonus |
Outstanding safety improvement by a team | Extra day off |
Monthly safety champion | Recognition certificate and parking space |
Adjusting Safety Objectives Based on Feedback and Results
Regular evaluation of safety performance is essential for maintaining an effective safety program. By analyzing feedback from employees, safety audits, and incident reports, organizations can identify areas for improvement and adjust their safety objectives accordingly. Continuous adaptation ensures that safety goals remain relevant and achievable, leading to a safer work environment for everyone.
Feedback from workers and safety teams provides valuable insights into the effectiveness of current safety measures. By acting on this input, organizations can address gaps, improve training, and refine procedures to enhance overall safety standards. Regularly updating safety goals based on real-time data strengthens a culture of safety and helps mitigate potential hazards before they escalate.
Key Considerations for Adapting Safety Goals
- Evaluate safety performance metrics regularly.
- Incorporate employee feedback into safety program adjustments.
- Monitor the results of implemented changes and fine-tune goals as necessary.
Important: Always base adjustments on data from safety audits, near-miss reports, and feedback from all levels of the workforce.
Steps to Refine Safety Goals
- Collect data from various sources such as incident logs and safety reports.
- Engage employees in discussions about current safety procedures and areas for improvement.
- Analyze the feedback to identify trends or recurring issues.
- Adjust goals to address the specific needs identified through feedback and data analysis.
- Communicate the updated safety goals clearly to all employees and provide necessary training.
Example of Safety Goal Adjustment
Previous Goal | Adjusted Goal | Reason for Change |
---|---|---|
Reduce injury rate by 10% in the next year | Reduce injury rate by 15% based on higher-than-expected injury frequency | Feedback indicated that current safety measures were not addressing root causes effectively. |
Improve training participation by 20% | Improve training participation by 30% after assessing the low engagement levels in previous sessions | Employee feedback suggested more engaging, interactive training methods were needed. |